Coconut has been a source of income for many South Indian farmers and dealers, and similarly, is a consumers’ favourite to beat the heat during the worst of summer days. However, many coconuts go waste after each season, owing to either excess of stock or simply because of going stale due to the harsh weather, which further affects the livelihood of the small and big farmers investing in this industry. On the other side of the consumerism, the fashion industry has been forced to rethink and reiterate its ways of functioning in order to become more conscious, as environmental and humanitarian sustainability has become the need of the hour, and the search for alternates that are more sustainable in nature is a never-ending process.
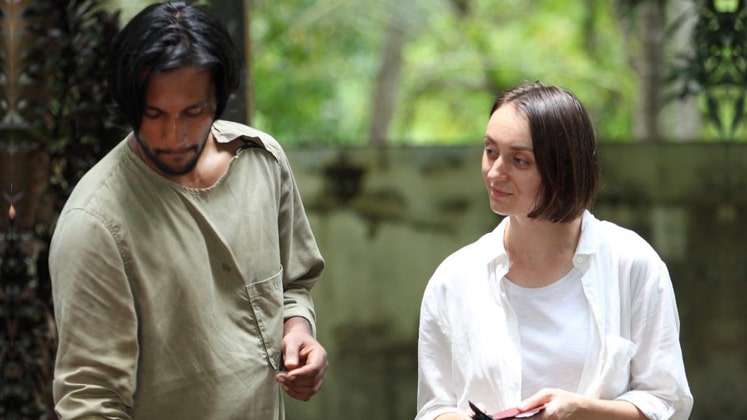
Bridging these two extremely different perspectives in the form of a genius innovation which was simply named as Malai were Zuzana Gombosova and Susmith CS, now identified as the transformers of the alternate leather material industry and the waste coconut industry as well. Zuzana Gombosova, a material researcher and designer from Slovakia and a graduate of MA Material Futures at Central Saint Martin’s College of Arts & Design, and Susmith CS, a Kerala-based mechanical engineer and product designer who graduated from IISc Bangalore together developed Malai, a biocomposite material made from entirely organic and sustainable bacterial cellulose, grown on agricultural waste sourced from the coconut industry in Southern India.
“Many wonderful designers, scientists, and makers are trying to respect and include nature and its harmony in their practice. We live in a time where new approach to fashion is needed, and we are happy to have been able to join this movement with Malai.” – Susmith CS
Talking about the journey of Malai, and their revolutionary product, Susmith says, “We have been working on developing Malai for two-and-a-half years so far. Our main inspiration is nature itself and its ingenious ways of solving problems and exhibiting beauty.” Zuzana also chimes in, “We started from scratch, basically working with the recipe in our kitchen. In collaboration with experts from various fields and driven by our own curiosity and trial and error process, we developed a flexible, durable biocomposite material comparable to leather, which is water resistant and contains absolutely no artificial ‘nasties’ that might cause any allergies, intolerances or illnesses. It is a completely vegan product and as such you could even eat it, although it’s way too pretty for that!”
Also Read: Is the pandemic hiking up the demand for everything organic?
How Malai is made
The company works with local farmers and processing units to collect and further harvest waste coconut water, which is otherwise disposed off, causing damage to water bodies as well as running soil by making them acidic. In fact, a single coconut-processing unit has the capability to amass about 4,000 litres of water per day that can be used to make 320 square meters of Malai.
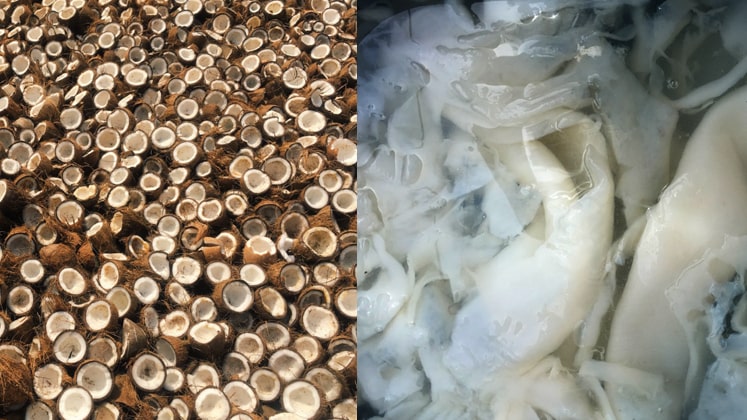
‘Malai’ directly refers to the creamy flesh of the coconut while the coconut water (a by-product from the harvesting of this flesh) sustains the bacteria as they produce the cellulose, which is then collected and refined until it becomes the finished material: Malai. It is a flexible, durable biocomposite material comparable to leather, but made with a very less impact to the environment by utilising waste coconut and producing vegan material.
The process of making Malai is ingeniously simple and involves an array of steps that start from the collection of ‘waste’ coconut water post harvesting of white flesh from inside the mature coconuts. Southern India’s coconut farmers and processing units are normally used to releasing the water into the drainage system, causing pollution of water and the soil to become acidified. “The water is placed into vats and sterilised, resulting in an energy-rich, entirely natural nutrient upon which our bacterial culture can feed. We combine the nutrient with culture and then just let the bacteria do its thing,” explains Zuzana.
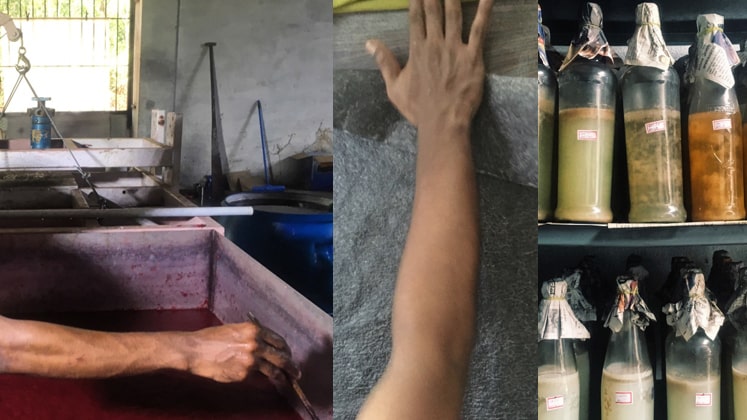
In about 12-14 days, the fermentation results in a sheet of cellulose ‘jelly’ called Bacterial Cellulose, a natural compound consisting of dense web of nano-fibres of cellulose. It grows in its pure form, and therefore, no chemicals are needed to be used to extract it as in case of plant-based cellulose. As per Susmith, Malai isn’t the only product where Bacterial Cellulose is used, as the “potential of this super material has been explored by scientists and designers alike and finds applications in food, cosmetics, medical industries as well as aeronautics!”
Post these processes, the jelly is harvested and refined, and further enriched with natural fibres, gums and resins to create a more durable and flexible material. It is then left to air-dry and softened using gentle water-resistant treatment, avoiding any plastic coatings or synthetic ingredients, and finally, ‘Malai’ is produced. The material is very customisable when it comes to weight and can be modified as per application, and the strength is directly proportional to the weight. Thinner weights are more flexible and softer.
However, maintaining a supply chain with clusters is identified as complex and rather slow, as Zuzana elaborates, “As of now, we are working with coconut processing units, but we would like to also incorporate copra societies and coconut farmers directly. Apart from coconut, we are establishing connections with banana cultivators to be able to collect fresh banana stems for fibre.”
The Malai Materials –
1. Malai soft (300-500 gsm)
Suitable for fashion application with smooth finish and soft feel, recommended to be backed with an adhesive lining to increase the strength. |
2. Malai medium (550-650 gsm)
Suitable for fashion accessories, stationary, packaging and furnishings application; has more textured surface finish, remains flexible and has a medium soft feel. |
3. Malai strong (700-1000 gsm)
Suitable for furnishing, interior surface design, stationery; more structural textures and has a rougher, more rigid feel. |
Malai is made in the form of sheets 120X80 cm large in three types of thicknesses and nine colour shades, with an average price of Rs. 3,000. Talking about the cost of sustainability and innovation, Zuzana expresses, “As a small-scale producer, you are trying to justify the value of work that everybody puts in, and conversely, the clients are requesting lower price. Our pricing is acceptable for markets in EU and US, but for Indian market, it might be high. Although in vegan leather segment, our prices are actually one of the most competitive.”
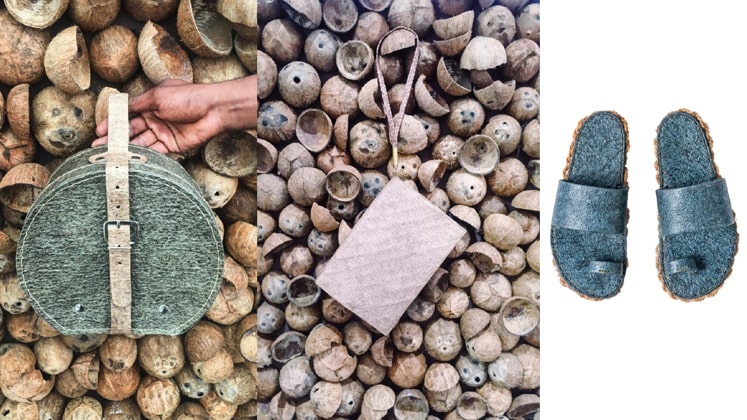
“Funding is an essential part of any start-up’s development, and being mostly self-funded, we decided to do a crowdfunding campaign to raise money for equipment needed to dry our sheets during rainy season, and secondly, to test the demand for products made of Malai and gain first ambassadors.” – Zuzana Gombosova
Also Read: Every bit counts: Redirecting fabric waste to craft new products
The Malai range of products
Being customisable, Malai can be produced in sheets with varying thicknesses and textures, and can be elevated to the next level by creating seamless three-dimensional objects using a moulding technique developed by the company. A range of colours can be achieved as well using mordant-free natural dyes, and it can develop a soft sheen or patina over time. Products made from Malai can last many years if properly cared for, and once ready to be disposed, can be placed in with your compostable rubbish to naturally break down, enriching the soils.
As per the duo, Malai performs the best while making bags being stiff and structural in nature. Susmith suggests, “We recommend 450 gsm for wallets and purses, 550 gsm for anything bigger.” The first collection made by the Kerala based Malai design studio was Fin[it]e, offering a range of accessories of unisex wallets, bags, backpacks and pouches offered in the range of their signature earthy colour palette. Produced in India, these pieces were first presented during Malai’s crowdfunding campaign at HitHit.cz in October/November 2019, and further went on to win the Circular Design Challenge – a competition awarding most sustainable and circular fashion projects/brands in India during the Lakme Fashion Week in February 2020, where it emerged as a winner owing to its inspiration of Kerala – land of coconuts.
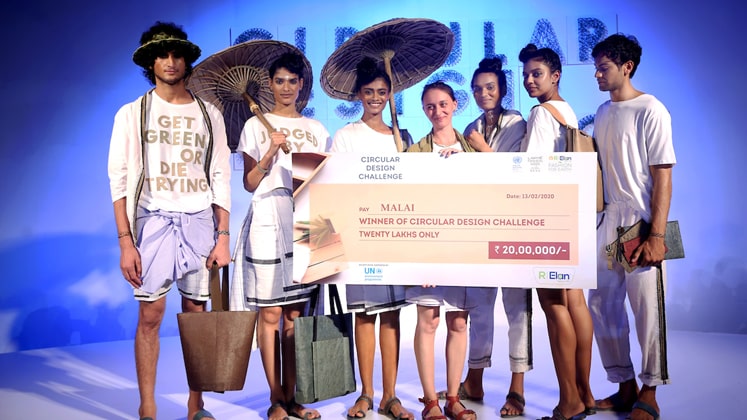
Previously, Malai studio has also worked with shoe designers Lucie Trejtnarova and Eva Klabalova who designed and produced various models of shoes, and later with a Czech company Kazeto as the material was ideal for their product range. They have also collaborated with a fashion designer Libena Rochova during a crowdfunding campaign where she created a versatile tote bag/ interior object with one-of-a-kind design.
A bright future
Winning the Circular Design Challenge has certainly put Malai, a PETA-approved label, on the radar, giving the initiative the traction it deserves after successful exhibitions at London Design Week and the Prague Design Week. The duo believe that Malai is at a stage where they need to grow and develop and seek ways to become more professional. Accordingly, this year they are installing new infrastructure which will enable them to increase capacity and achieve more consistent standards throughout their offerings. Susmith further avers, “We will also work further on the research part of our work to improve material properties. Apart from that, we would love to work with universities and companies which truly seek to adopt sustainable materials in their product portfolio. And last but not the least, we are looking for further funding.”
Calling sustainability an elitist movement, Zuzana says that cost is inevitable while bringing up innovative and new products at the beginning, and ideally, sustainability should be about good practices that promote equity and harmony, not elitism. She also identifies the vegan fashion space in India at a baby stage; however, a few brands exist which identify with the movement here. “More than that, it is a demand from Indian manufacturers who make products for export though,” she says, further concluding, “Though there is still quite a communication gap between veganism and sustainability, they are not interconnected. Many vegan brands will choose PU and PVC materials in the name of saving animals, but will completely disregard the fact that these are not exactly great materials for the environment.”
Also Read: Top Trends in Sustainability in a series of 4 trend features by Apparel Resources