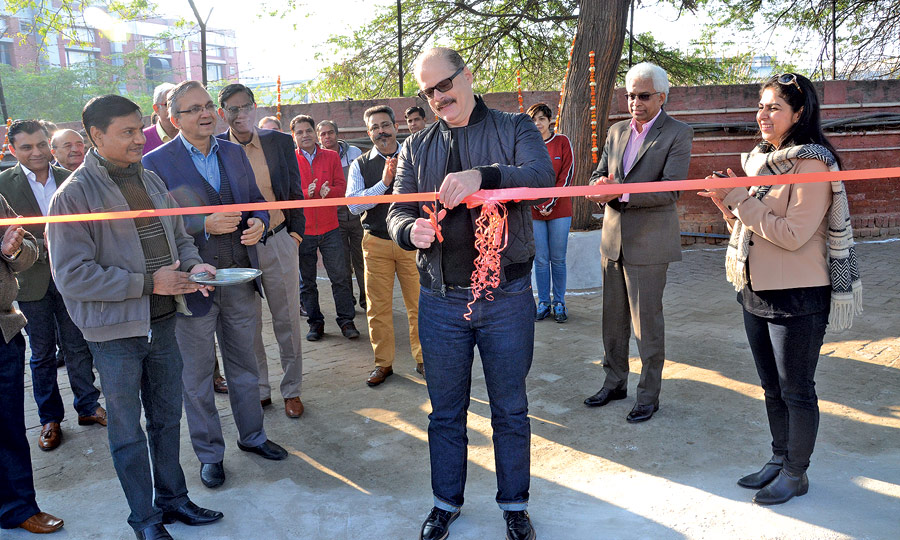
One of the most respected apparel export houses in the Delhi-NCR region – Matrix Clothing, Gurgaon – led by Gautam Nair, has moved forward on the ‘Green’ route by installing a solar power plant of 258 KW at its factory. The plant generates 0.33 million units a year which is near about 10 per cent of the company’s total power consumption. Now 67 per cent of the energy needs of the company are met by its own solar/ wind generation.
Concern for environment is a cornerstone of the company’s individual and business philosophy. From ensuring wastage of resources to investing in infrastructure that is environment-friendly, the company does whatever it can for the environment. It is perhaps the only apparel exporter of India which uses earth (prithvi), wind (pavan) and fire (agni/ surya) for energy production and saving.
The installation of solar power plant is now necessary for factories in Haryana as per the order passed by the State Government of Haryana in September 2014. A notification, for the installation of rooftop solar power systems for commercial buildings, having load connection of 50 KW to 1 MW, was sent across the state, making it mandatory for such factories to produce 5% solar power of the total requirement or 10 KW, whichever is higher. The project cost of installing solar energy was Rs. 2.5 crore.
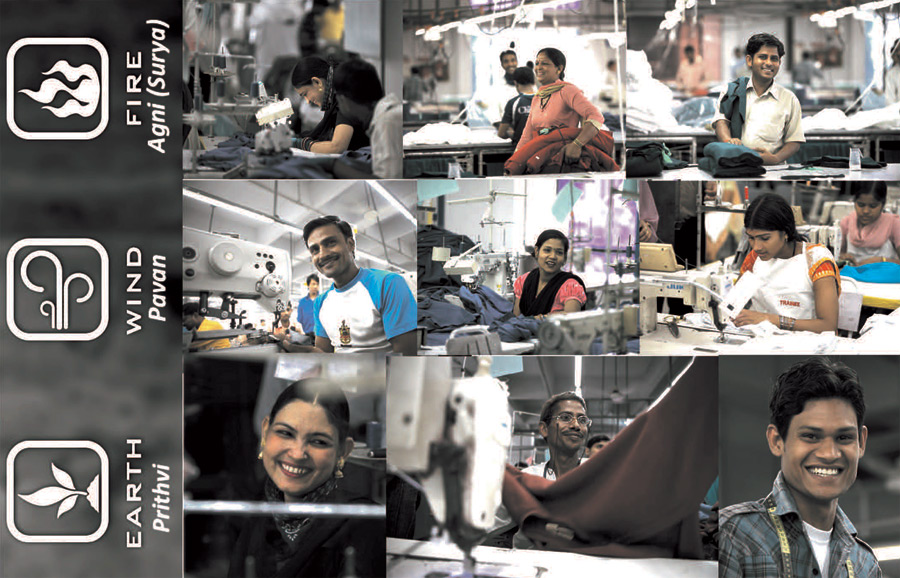
Vipin Gupta, AVP, Personal & Admin, Matrix Clothing informs, “As part of Matrix’s commitment to the renewable energy initiative, the company owns/operates two wind turbines (each generating 600 KW of power) in Gujarat, which supply two million units of electricity to the Gujarat Electricity Board.” He further adds, “We are using around 1,000 sewing machines with direct-drive motors instead of clutch motors. Further, 600 clutch motors will also be replaced in the coming months. The company’s replacement of 160 ironing stations from electric-heated to stem-heated help save 1,90,000 units per year. Similarly, window exhaust fans (380W each) have been replaced by 50 roof-top non-electric extractors, resulting in saving of 23,000 units per year. Also, 5,400 tube lights (T5-54 watt) have been replaced by 28 watt energy-efficient tube lights which helps save 4,20,000 units per year. Now moving forward, these T5 tube lights of 28 watt are being replaced by LED lights of 16 watt. Apart from these initiatives, the company also runs an ‘energy-efficiency’ awareness programme.”
It’s not only about electricity for Matrix Clothing, the apparel exporter is equally concerned about water saving and its reuse. It has set-up an ETP (Effluent Treatment Plant) with the capacity of 120 KLD and uses treated water for other purposes like in toilets. The company also has a Sewage Treatment Plant, and the treated water from here is used for horticulture purposes. To control noise pollution, the Indian apparel exporter has an acoustic chamber for an old DG set of 500 KVA, and has installed Silent DG of 500 KVA.
Moving forward on the green path, the apparel exporter has planted 369 trees at its campus and has four rainwater harvesting pits of 1,53,000 lt. holding capacity, with a bore size of 4-6” that go down to a depth of 250 feet. In fact the company claims that it is the first factory in the area to install rainwater harvesting in its premises.
Manufacturing knitted polo shirt and embellished ladies garments, BSCI & SEDEX compliant Matrix Clothing has a workforce of 5,000 and an export turnover of US $ 55 million (Rs. 356 crore) for the fiscal 2014-15. The company has a long client list including Li & Fung, Hugo Boss, Debenhams, NEXT and Nautica. It also runs the “Apparel Skill Development Academy” (ASDA) which focuses on training and providing necessary basic skills in the various aspects of apparel manufacturing. The company also supports Iimpact and Salaam Baalak Trust.
Apart from such big initiatives, the company also focuses on small but equally important points like paper saving & re-cycling by making writing pads from rough paper, re-cycling of printer’s cartridge & ribbons by refilling, using refilled sketch pens/white board markers, reduction in consumption of diesel fuel in boiler by using waste petroleum products, reduction in consumption of diesel fuel in diesel generator (DG) set by using independent feeder line of power and waterless urinal. Similarly, it has leakage monitoring control on regular basis. It has the system of replacement of conventional bibvalves by push valves & self-stop ones in almost all taps, to stop leakages/drip wastage.
Commenting on what drives the management at Matrix Clothing towards sustainability, Vipin shared, “We at Matrix believe in ethical and environment-friendly business operations rather than just doing business. We started this initiative towards renewable energy 4-5 years ago without any compulsion or mandatory requirement by the Government. Buyers too support such initiatives comprehensively which leads to establishing a credibility; besides of course, we get good business opportunities also.” Even the workforce at the company is motivated and proud to be working with a company that is sustainable which is encouraging for the management to move even further beyond. “We have a plan to put up a ZLD (Zero Liquid Discharge) process in the near future to re-cycle the water consumption which will make us less dependent on the water supplies from the authorities or ground water extractions,” concludes Vipin.