Even as the Indian garment industry struggles to regain its footing in the fast changing international economic scenario, its counterparts in the textile industry seem to be faring better. The 8th India International Textile Machinery Exhibition (INDIA ITME 2008) to be held from 15-22 November, 2008 in Bangalore gives an indication with the participating international companies presenting their machines for not only spinning and weaving, but also processing and finishing, signifying that capacities are being built.
The Fair will offer a once in 4-years opportunity to the Indian textile industry as well as the students to see in operation the latest the world has to be explored. StitchWorld previews some of the leading international companies that will be participating at the event.
1) Benz to Display Technologies from Masias, GMI and Meca
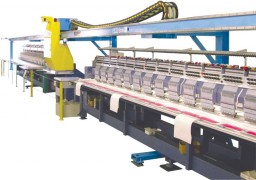
Technology supplier Benz Embroidery Services are the authorized sole representatives of international brands such as Masias Maquinaria from Spain, Meca SPA from Italy and GMI, also an Italian company. At ITME, Benz will be hosting Principals from all three companies to demonstrate their technologies.
At the event, textile machines manufacturer Masias will present the Direct Feeding System SAD MF connected to a multineedle quilting machine from Meca. This machine is designed to feed directly micro-fibres or standard polyester fibres from bales to a multineedle quilting machine with a perfect synchronization and enabling the formation of a regular and controlled pad. The Techna Multitech Encording machine from Meca on which this will be displayed, is a unique multineedle lock stitch quilting machine with rotating hooks working continuously from roll to roll. The easy setting of its interchangeable dedicated robot feet allows the execution of different programmes: standard, embroidery-like, cording and ri-ri. This machine allows better capacity for producing twin-line patterns, jump and tack with single or twin-line, isolated patterns and embroidery line patterns by automatic application in continuous, roll to roll, of cords, ribbons, tapes and passementeries on quilted articles as well as on simple fabrics, jeans and sky, voiles and chiffons, home textile articles, curtains, garments, lingerie, etc.
GMI will put on display it’s new GMI laser III machine with a 3-axis galvanometric head. The focus has been on the dynamic beam expander with special mirrors and to guarantee a better spot under the same working area. This gives more definition on the cutting, more speed and less burning for the same fabric cut. It has a big working area of 500X500 mm with a very small spot cutting point and the facility of focalization with dynamic beam expander. The variable field allows working with the optimal field according to the kind of fabric to cut and permits more vertical cutting in smaller field.[/tab]
2) Monforts Focuses Upon Energy Solutions at ITME
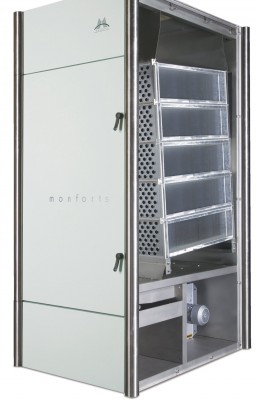
German company Monforts is a leading manufacturer of machines for dyeing and finishing of knitted and woven fabrics. The company is constantly innovating and remodelling its technology to address the key issues affecting the industry at a given time. This year the focus will be on conservation of energy. Today energy represents more than 60% of the total cost of a dyeing and finishing system over a period of time. To meet this challenge, Monforts will be displaying its tried and tested solutions at ITME.
The new Heat Exchanger can be integrated into the roof construction of most Montex stenters for heat recovery. The exhaust air heat is converted in the heat exchanger to heat the fresh combustion air which enters the inlets of the stenter through integrated fresh air ducts. Up to 60% of the fresh air required by the stenter can be preheated, providing an energy saving of between 10-30% depending on the production process. Another product, a stand alone Energy Tower, has been designed to stand alongside the stenter or hotflue. It features five integrated heat recovery modules which capitalize on the high temperature of the exhaust air, giving savings of up to 30% in energy costs.
3) Xetma Prepares to Showcase its New Optisystem XEB HIGHTOUCH Machine
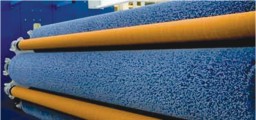
German Swiss Venture, Xetma Vollenweider is a brand synonymous with textile finishing systems, and especially dry mechanical finishing. This ITME the company will be presenting an overview of its range of products and services in surface finishing systems, including machines for brushing and emerizing, raising, shearing and cloth cleaning. However, keeping in mind the ever increasing demand for value-added technologies in brushing, Xetma has decided to put on display its latest machine system Optisystem XEB HIGHTOUCH. This machine sets new standards in textile finishing, both in terms of production performance and also the quality of the surface effects.
The combination of brushing and emirizing creates soft touch effects with an incomparably high density and a tangibly softer feel, called the ‘Rose Petal Touch’. This combined technology of brushing and emerizing rollers used alternatively gives much higher production speeds of up to 40 m/min.
4) Groz Beckert to Present its Latest Litespeed Needle
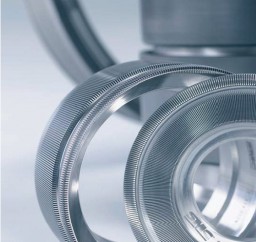
With an experience of over 150 years in producing needles and precision components for the apparel and textile industry, Groz Beckert is constantly challenging its R&D for new designs. This year the company will display its new Litespeed® needle and SMC precision cylinders along with the other product range.
Litespeed® is the latest generation of needles for high performance circular knitting machines with a tapered shank to reduce the lateral friction between the needle and trick wall. Due to this, the lubricant can flow in easily and the Litespeed® needle acts like an oil pump, distributing the lubricant between needle shank and trick wall and guaranteeing an ideal oil film. This not only further eases the friction but also reduces wear and temperature as well as needle and energy consumption. The Litespeed® needle also facilitates the machine cold start and reduces machine noise.
5) Rieter Brings Machines for Spun Yarn and Non Wovens
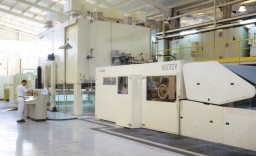
Swiss company Rieter Textile Systems is the world’s only manufacturer of technology covering the entire spinning process for yarns from both natural and manmade fibres including nonwoven, a segment with numerous applications ranging from the hygiene to the industrial and the medical sector. The company offers a range of products which cover everything from raw material to end-product, subsystems, machines, components, wear and tear parts as well as spare parts to accompanying services from pre-sales to after-sales. Its complete range as well as after-sales-services are handled in India by its local offices.
This year Rieter will present its systems for the production of spun yarns and nonwovens. On display will be carding, combing, ring and rotor spinning machines for spun yarns. However, in appreciation of the growing popularity of nonwovens, Rieter will also showcase its JETlace series of machines for production of nonwovens. JETlace® 3000 is custom designed for producing hydro-entanglement fabrics from 30 to 500 gsm. It can entangle all kind of fibres as well as spun laid filaments. JETlace® Essential is ideal for wipe production: It is configured for lightweight fabrics from 30 to 80 gsm. JETlace® Avantage can easily produce 5000 tonne of fabric of 30 to 120 gsm per year at a competitive price. This machine is based on European design and is a perfect tool for emerging markets to start spunlace nonwovens production.[/tab]
6) Janaksons International to put up Catalogue Show of Flainox Machines
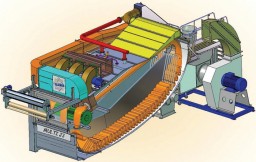
Janaksons International has, for the last two decades, dedicated its services towards providing knitting technology for the Indian textile industry. The company is the agent of Japanese company Shima Seiki, manufacturers of flat knitting and seamless machines, and CAD/CAM technology for the knitted product line. Having gained the confidence of its customers through its after-sales-service, the company has added another feather to its cap by a successful tie up with Flainox s.r.l. Italy, producer of machinery for the dyeing of garments, hosiery and seamless, to represent them in India on an exclusive basis. Flainox specializes in rotary dye extractors which can capably perform to give good results in all types of fabrics; whether cotton, polyamide or polyester.This year at ITME, Janaksons will put a catalogue show where technologists from Flainox will interact with the visitors to talk about three of its machines – EVO-2, NRP/HT and Multifinish. The models NRP/HT and EVO-2 are rotary dyeing machines for piece goods, seamless and bath-matts. In EVO-2, maximum temperature attainable is 105°C and the machine is available in 60 kg, 120 kg, and 180 kg. NRP/HT is suitable for dyeing of 100% polyester: It can attain a maximum temperature of 1350C and is available in capacities of 90 kg and 180 kg. The Multifinish is a special air finishing machine used to enhance fabric appearance and feel. It handles fabrics in rope form by exploiting the kinetic energy generated inside a Venturi pipe. It can also do dry treatments with or without steam injection, dry after foulard impregnation, with processes with chemicals, enzymes and softeners and caustic, resins polymerization and chemical treatments. The machine is available in different capacities: 240/320 kg, 360/480 kg and 440/580 kg.