Over the last 20 years, there has been a dramatic technical development of machines and software in the production of knitted fashion garments, especially flat knits. These developments have made it possible to rationalize design and production of knitted garments in today’s world directly on the knitting machine reducing the number of post-knit processes such as cutting and sewing. Cut & Sew, Fully Fashioned and Seamless are the various types of technologies that exist today for knitwear production; choice of appropriate technology depends on style, lead time and cost. In this article Meeta Gawri, Assistant Professor, Northern India Institute of Fashion Technology, Mohali explores options…
This study compares three different methods of producing flat knitted garments, viz. Cut & Sew or Stitch shaped, Fully Fashioned and Seamless. In this study, two crucial elements of production for any product have been undertaken, i.e. time and cost. To have an unbiased comparison between the three methods, the style and specifications of the garment were kept constant making it easier to reach the conclusion. In this study, time analysis of the operations in the three systems has been taken into consideration.
The manufacturing process of knitted garments can be divided into four different production methods – Fully Cut; Cut & Sew/Cut Stitched Shape; Fully Fashioned Garment; and Whole Garment/Integral/Seamless Knitted Garment. While fabric for fully cut garments is invariably knitted on circular machines, the last three are specific to flat knits. Hence, the comparative study shall take into consideration only these three methods.
Cut & Sew / Cut Stitched Shape
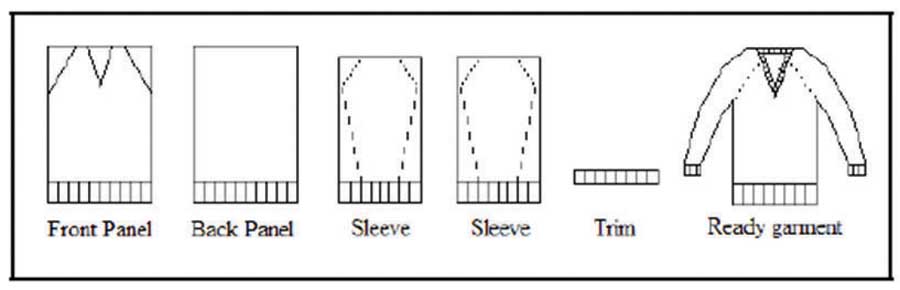
Cut & Sew is the most conventional and common method for production of flat knitted garments (Picture 1). Panels for front, back and sleeves are knitted in a rectangular form and then cut in the required shape in the cutting process. The pieces known as “Blanks” have the lower edges sealed with a structure known as “Welt” that prevents laddering and distortion of waistbands and cuffs. After the cutting process, the panels are sewn together with separately knitted trimmings and pockets to complete the garment. Both cutting and sewing are post-knit processes. With Cut & Sew, up to 20% of the original fabric may go to waste as cut-loss. The advantage with this type of production is that it could be done on all flat knitting machines, including old models without computer processing systems.
These blanks require minimal preparation for seaming. Cutting involves trimming of length and sometimes width followed by cutting of neckline and armholes, lower arms and shoulder shaping.
Fully Fashioned Garment
Fully Fashioned or shaping is a method of knitting production where the front, back and sleeve pieces are knitted in the right shape directly in the knitting machine (Picture 2). The cutting process is at a minimum or totally eliminated, but some post-knit cutting can still be necessary.
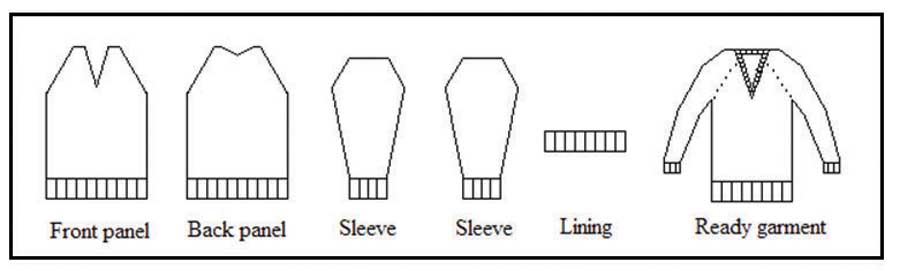
Trimmings and pockets are knitted separately and sewn together with the rest of the knitted pieces to complete the garment. The benefit of this production method compared with the Cut & Sew method is that cutting is eliminated or at a minimum, and that the material consumption is much lower due to lower cut-loss. Both material and labour costs are saved in comparison to the Cut & Sew production method.
Whole Garment/Integral/Seamless Knitted Garment
Integral knitting means that trimmings, pockets, buttonholes and other accessories are directly knitted in the fully fashion produced panels. With this technique there are fewer post-knit processes such as cutting and sewing (Picture 3). Compared with Cut & Sew and fully fashion production methods, savings can be in both cutting and sewing. In addition the quality and final appearance of the ready garment can be improved by this method of integrating accessories in the panels directly in the knitting process.
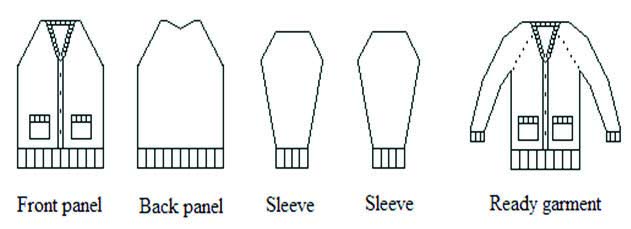
All yarn in the entire garment comes from the same yarn cones, which enables higher quality. Due to the seamless technology the garment could attain a perfect fit and be comfortable to wear. This technology makes it possible to produce “on-demand knitting”, which could shorten production lead time considerably.
Comparative Study
In this study the context is the production method and technique and the boundaries are the interaction between the two most important constraints: cost and time. For keeping the calculations unbiased regarding time and cost, garments style is kept constant for every method of production. In total two styles have been undertaken, V-neck T-shirts for men (Picture 4) and High-neck T-shirts for girls (Picture 5).
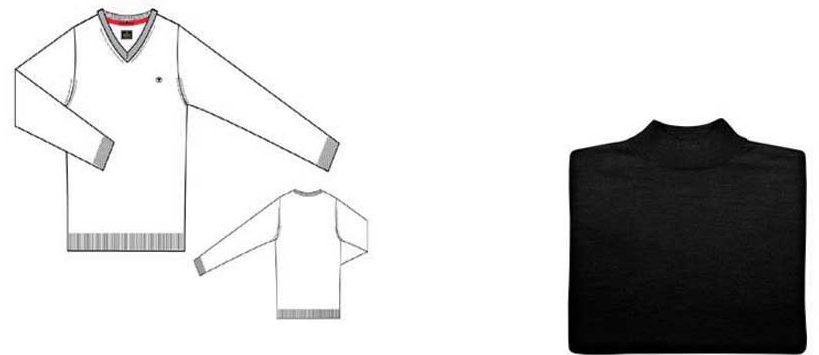
The operation breakdown for the 3 methods was done separately. A total of 15 readings for each operation under this study were analyzed and then a comparative analysis was done.
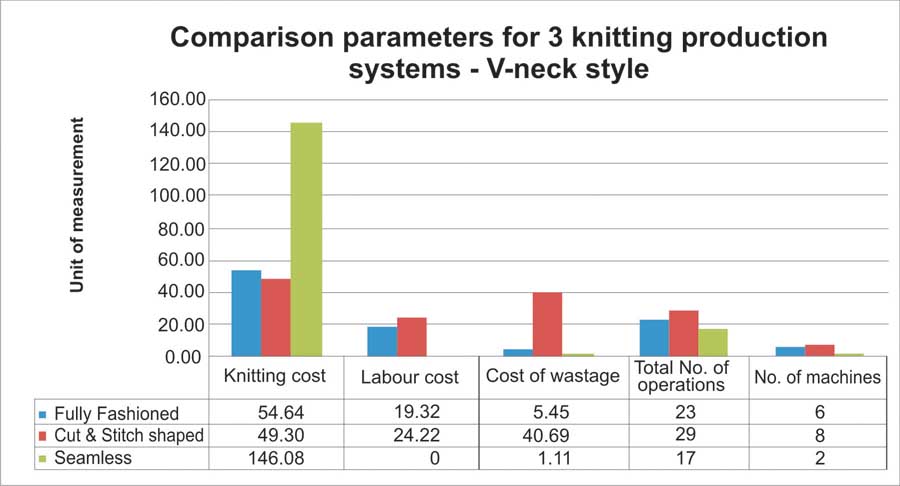
The comparison was done on the following macro parameters:
- Knitting cost;
- Labour cost for Cut & Sew process;
- Cost of yarn wastage;
- Number of operations involved; and
- Number of machines (not common to all)
From Chart 1, it can be perceived that for V-neck T-shirt style, knitting cost is highest in Seamless and least in Cut & Stitch shaped. Whereas labour cost, wastage, total number of operations and machines used for uncommon operations is maximum in Cut & Stitch shaped.
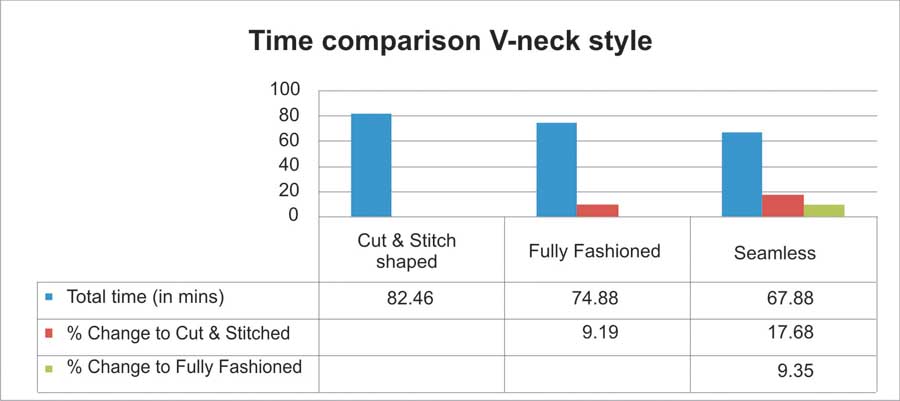
From the Charts 2 and 3, we can see that in terms of cost, Fully Fashioned method is beneficial while in terms of time Seamless method is beneficial.
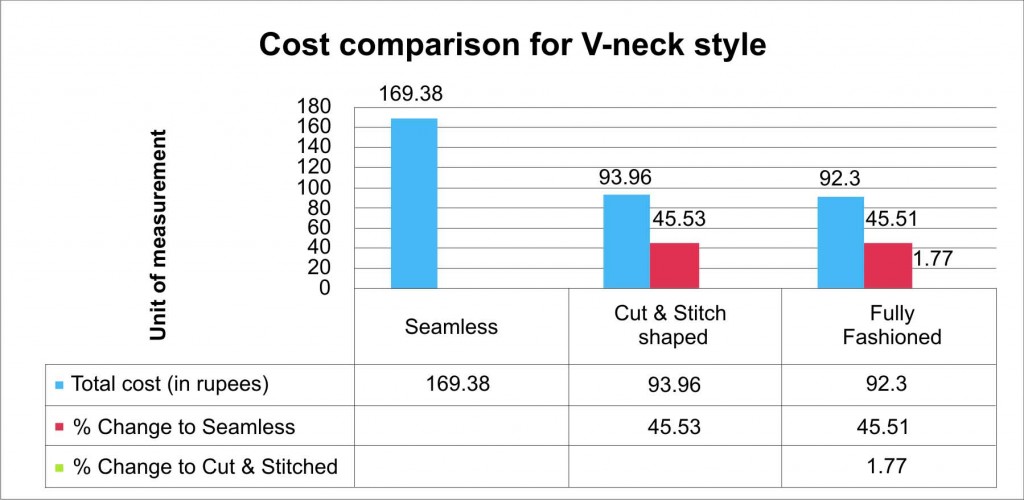
To summarize, we can say that the total cost of garment is highest in Seamless and least in Fully Fashioned garment while time taken to complete the garment is highest in Cut & Stitch shaped and least in Seamless method (Chart 4).

When we do the similar analysis for high-neck style, we see that for high-neck T-shirt, knitting cost is highest in Seamless and least in Cut & Stitch shaped. Whereas wastage, total number of operations and machines used (for uncommon operations) is maximum for Cut & Stitch shaped (Chart 5).
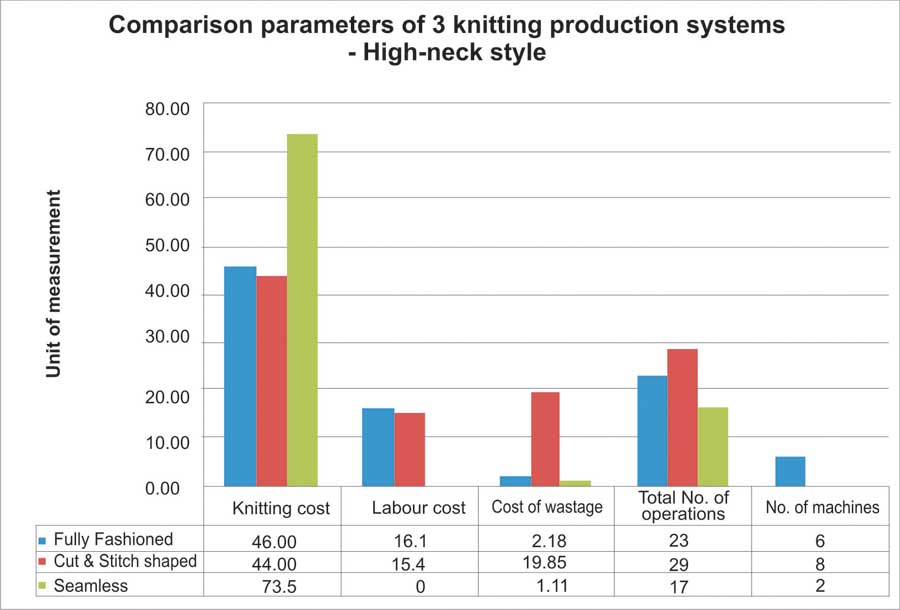
From the Charts 6 and 7, we can see that like in the V-neck style, high-neck style also, in terms of cost, is most beneficial in Fully Fashioned method; while in terms of time, Seamless method is beneficial.
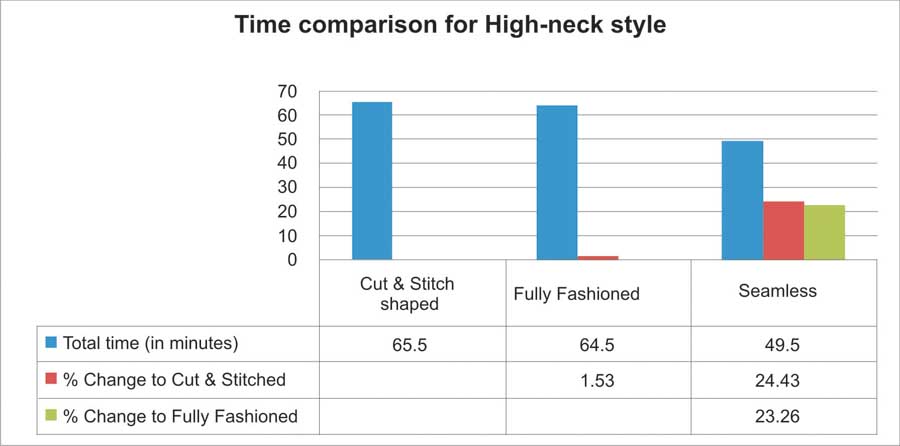
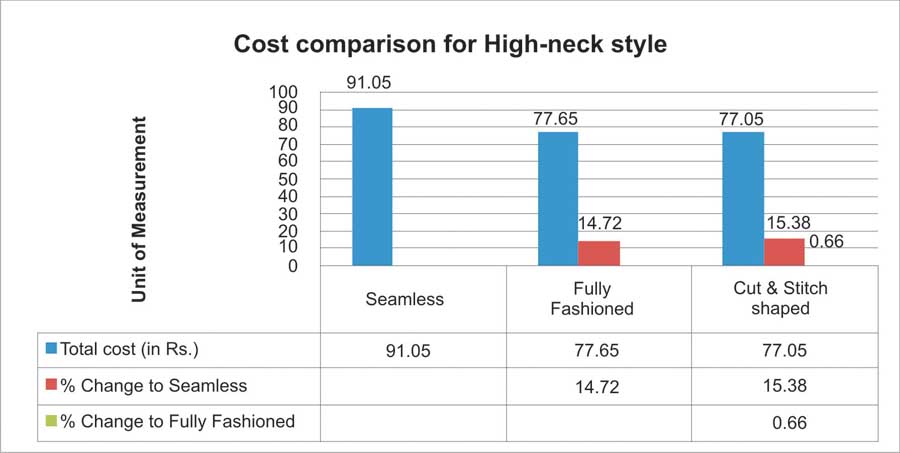
In this case, we can also say that in high-neck style, the total cost of garment is highest in Seamless while time taken to complete the garment is highest in Cut & Stitch shaped and least in Seamless method (Chart 8).

Is Seamless a Viable Option…?
The advantages in Seamless production method as compared to traditional production methods such as Cut & Stitch and Fully Fashioned are that there is time and cost savings in the time-consuming post-knit operations such as cutting and sewing. Also there is lesser wastage of yarn as the garments are made directly on the knitting machine as a result no cut-loss is produced. Besides, Seamless garment involves less labour cost and only a few machines. Even the number of operations are reduced which is possible only in this style of production.
The real benefit of the complete garment technology, as discussed in this paper, comes when this technology is implemented for those products or garments which is having very intricate knitting-structural-designs. This is important because in a fast fashion supply chain for knitted products, time to market for the products is essential. The complete garment technology makes it possible to reduce time for production in the supply chain. Processes are removed and non-value added time between processes is eliminated. Complete garment technology implemented in an effective logistics system could make the order fulfilment lead times shorter.
However, the only disadvantage is the high cost of machinery, being a new technology, which increases its knitting cost. The same can be justified based on the working life of the machine, the precision and the quality of the output and above all the lesser dependence on the manpower.
Considering the high cost of machinery in complete garment system, manufacturers prefer the Fully Fashioned production process because of reduced knitting cost, reduced labour cost and lesser number of machines used with only a few operations involved. Although complete garment system and Fully Fashioned method have advantage over the Cut & Stitch shaped method, we cannot eliminate this method completely. More so as there are certain styles which can only be made by Cut & Stitch method due to styling and design, more number of panels which are difficult to knit in perfect shape in the other two methods.
Conclusion
From the above explanation, it can be concluded that –
- The knitting cost is the highest in seamless garment (due to the expensive machinery and more time taken), and minimum in case of Cut & Stitch shaped method (due to rectangular panels being knitted);
- The labour cost (uncommon processes) is the highest for the Cut & Stitch shaped (because of maximum cost in marking and cutting of the patterns which is not so in case of Fully Fashioned and Seamless methods). However, in case of high-neck style, it is lesser for Cut & Stitch shaped because of the process of overlocking of the entire garment.
- Yarn wastage, total number of operations and the number of machines (uncommon operations), is highest in Cut & Stitch shaped method.