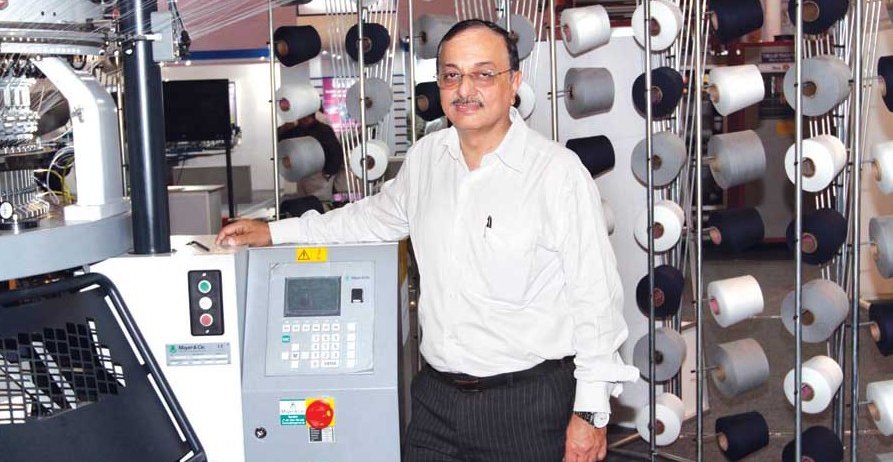
Productivity, flexibility and quality assurance are the factors that have made an impact on all the major knitting machine manufacturers and knitting accessories suppliers and that can be clearly seen in their latest offerings. Among knitting machine manufacturers, Mayer & Cie, Santoni, Pilotelli and Terrot-Voltas have added an application and/or device to their products that enhances the productivity while the machine remains flexible to handle multiple styles and also ensures quality first time. Among knitting accessories suppliers, Groz Beckert and Memminger have complemented their offerings to boost quality with high productivity. Team StitchWorld reviews latest productivity improvement tools and solutions offered by the knitting machine manufacturers.
Mayer & Cie: Flexibility with Productivity
Fashionable stripes and high performance for basic fabrics is possible from Mayer & Cie knitting machine “S4-3.2 R”. This model knits with 4 to 6 colours across 1.6 feeders per inch. It is also equipped with the well proven MCT striper technology patented world-wide by Mayer & Cie with the focus on optimal function, MCT striper units have significantly fewer parts than usual. All striper fingers are used for the colours, and the stripe-out function takes place specifically in the striper units. With stripes over 2 feeders, yarn clamps transfer the yarn from one to the other feeder.
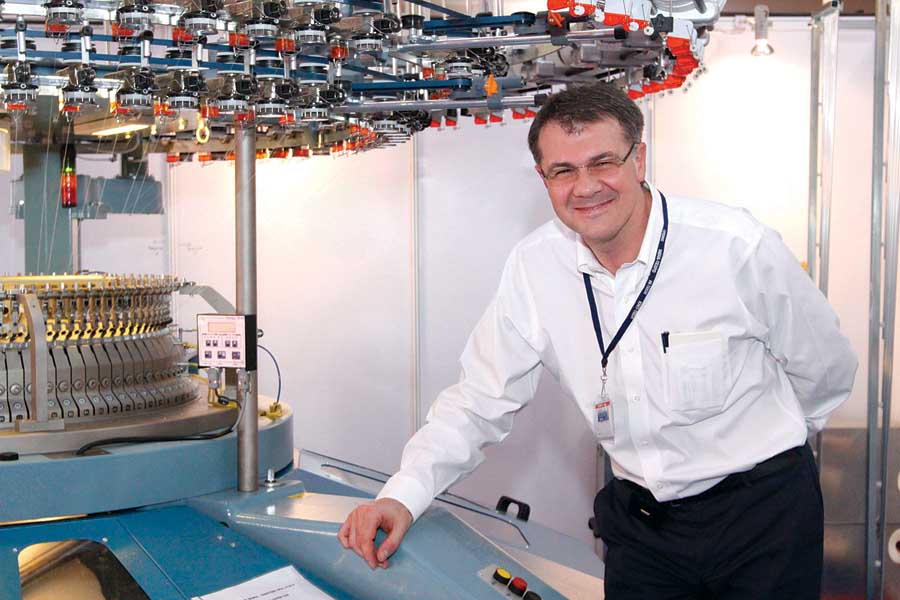
Flexibility with high productivity can be achieved by simply replacing the striper non-knit feeders with knitting feeders that immediately gives 3.2 feeders per inch for basic single jersey fabrics. With 26”, 30” and 34” diameter cylinders and high speed changeable gauges of E 18 to E 32 and E 36, the machine runs at a speed of up to 0.9/1.4 metres per second.
“In comparison to the normal machine of 34” cylinder diameter having 54 feeder stripers, we offer 108 feeder stripers that double the production while striping with 3 colours,” says Rakesh Bagga, GM, Batliboi, the representatives of Mayer & Cie in India.
This easy to operate and maintain machine is incorporated with a deflection winder mechanism and trapezoidal spreader for fabric bails of up to 480 mm in diameter. For crease-free production the Made-in-Germany version of machine is enabled with a choice of open width frames for ease adjustment of fabric width as per requirement, while the Asian version without the adjustable width option has been successful in this region. Both open width frames can be converted to tubular deflection winding.
“With a fabric fault of around 0.5 per cent and a minimal breakage of any yarns type, the return on investment is very fast,” says Bagga. He adds, “Being economical, highly productive and more flexible, the machine has already started getting good response in India.”
SANTONI: Patented Technology for better Productivity
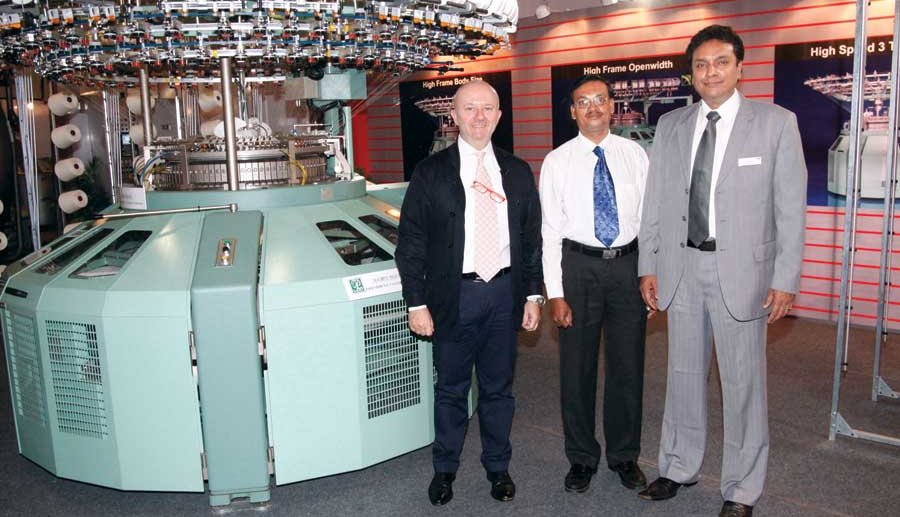
In India SANTONI has just launched its single jersey high speed ATLAS series machine having a unique system of knitting without sinkers and enabled with a special patented “Comb” which allows the production of excellent fabric with increased productivity as compared to conventional single jersey machines with sinkers.
Instead of sinkers, the machine is equipped with special holding-down jacks (patented by SANTONI) which allows the machine to run at full feeds and make the knitting re-start fast and easy after a fabric press-off. The stitch formation is undistorted from any mechanical movement and the risk of any sinker line on the fabric is totally absent.
Any type of yarn from cotton to synthetic can be used for knitting with some optional attachments for special yarns/functions like lycra feeding units, CAMs for pique/mock interlock and electronic controlled take-down system.
The CAM boxes are very lightweight and made out of a special aluminum alloy named “Ergal” having a great heat dissipation property, while the yarn carrier head is made of Black Zirchonium that allows a better visibility of the elastomer.
The machine is available in tubular as well as open width frame and is around 15-20 per cent expensive than normal machines with sinkers. “The quality of the knitted fabric and the early return on investment (approx 1.5 years) of the machine makes it a first choice of exporters, as some machines are already booked and in future expecting even a better response from the market,” says Gianpiero Valsecchi, Sales Area Manager, Santoni.
Pilotelli: Quality with Productivity
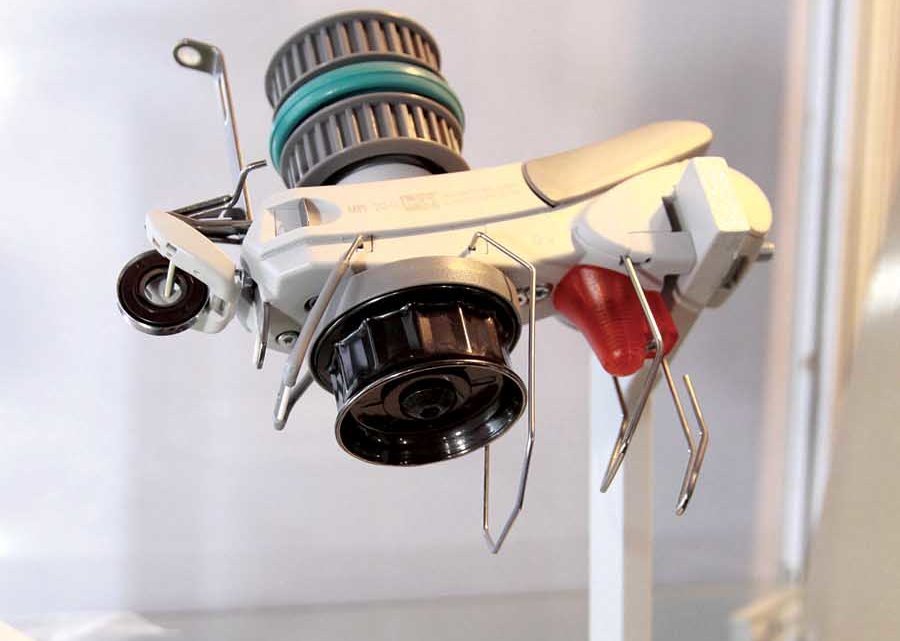
Pilotelli, since 1983 produces circular knitting machines of high quality and is specialized in lycra fabric knitting machine. Its latest model “J-3.0 T.A.3” runs at 35 RPM while other normal open width machines can run up to 30 RPM only. A scanner attached to the machine identifies various types of defects in the fabric and allows the machine to stop automatically on such identification.
Various small new techniques have been added instead of any one big change to make the machine more user-friendly like its speed has been increased, improved cleaning system that keeps the textile head, needles and sinkers perfectly cleaned and oil stream lubrication without fog formation with very low air consumption.
The machine is designed after considering the operators’ need that could deliver ease of access to the needles and the yarn feeders, high visibility of the needle, sinker shape and the area of the knitting formation, ease of access to all the adjustments, limited height from the ground and continuous electronic speed adjustment. All these user-friendly additions make it possible for 3 operators to function on 5 machines at a single time.
“An operator spends around 20 minutes in cleaning the machine at the end of each roll, and if in the whole day he changes 20 rolls then this leads to unproductive time of 200 minutes. To overcome this wastage of time, we have upgraded our cleaning system to a level where in at least 150 minutes per 20 rolls is saved that indirectly increases the productivity of the operators,” says Perumal Nagaraj, Asst. Manager Sales, Textile Engineering – Circular Knitting, ATE Enterprises, the representatives of Pilotelli.
Further, while normal knitting machines need periodical maintenance after 5 to 8 tonnes of production, the new Pilotelli machine only requires a periodical maintenance after 20 to 25 tonnes of production, again saving critical time on ‘non-productive’ activities.
Terrot-Voltas: Enhancing Productivity
Terrot’s single striper machines with 4 or 6 colour stripers and up to 4 needle tracks provide decisive advantage in production and are available in two models of “S4F348” and “S6F348”. These models have standard C-frame for 500 mm fabric rolls and an industrial C-frame for 800 and 1050 mm fabric rolls; latter being an optional frame. These frames are having hand levers, uniwave spray oiler, pulsonic 5 oiler, oil bath for cylinder bearing and the striper drive system. Up to 4 needle tracks are also provided in the cylinder. “We have introduced a 30 diameter machine that produces 250 kg of fabric per day, which is a production increase of around 100 kg per day as compared to earlier models,” avers Franz Hudi, Area Sales Manager, Terrot. Terrot is being handled by Voltas in India.
Some technical changes have been made in the machine especially in the CAMs’ arrangement so that instead of earlier CAM arrangement of 96, the new formation has CAM arrangement of 48. Exchange CAMs are now available for 3 positions Knit-Tuck-Miss. These few changes have increased the speed and the quality production of the machine.
Enabled with a frequency controlled drive of 4 KW, digital inverter and a controlled voltage of 24V, this machine of 30” diameter runs at 28 RPM. Pressure free fabric gets wind up on an automatic device and can be taken-down mechanically with 3 rollers. It also folds automatically after being knit and get placed in the available fabric basket.
“More than 50 designs can be inserted in the control that changes according to the changes made in the CAMs while the colour selection for the same designs has been made fully computerized,” says Hudi.
Knitting Machine Accessories
To keep pace with the evolving speed and versatility of knitting machines, accessory manufacturers and attachment manufacturers too are introducing many improved and innovative technology. Two important players Groz-Beckert and Memminger are among the most upfront…
Groz-Beckert: Keeping pace with Speed
A new development from Groz-Beckert, ‘Litespeed’, is a patented new knitting development for high speed large diameter circular knitting machines. Needle shank’s thickness is partially diminished while keeping the dimensions exactly same to the corresponding standard needles. This reduces the machine temperature and the energy consumption by up to 20 per cent and also increases the productivity of the machine.
The company also provides “Knitting Cylinders with Sinker & Dial Rings” with around 60,000 cylinder types to suit more than 2,000 machine models. Diameter and gauge ranges from 7” to 60” and E 3 to E 66, respectively. Slot by Slot exemplary gauge accuracy avails the flawless knitting and highly uniform fabric quality.
Trained and experienced technical team of the company is always available for comprehensive and competent advice for drawing, fitting and maintenance of cylinders. “With our one office in Tirupur, we are also having many agents for the local knitting and sewing machine needles in different parts of the country while all the imported needles are supplied directly, with no agents in-between,” says S. Kumar, Manager Sales (South & West India) Knitting Machines Division, Groz Beckert.
Memminger: Online Quality Inspection
Memminger has introduced a fabric scanner “LMW 3” that is available in various versions and is suitable for mounting on to different circular knitting machines producing various types of plain fabrics. On detection of any fault (like needle lines or holes), the LMW 3 stops automatically.
The LMW 3 consists of a controller and a scanner head. The scanner head lies on the fabric surface and uses the light reflection principle to detect faults. The light emitted by the scanner is reflected back by the fabric and the resulting signal received by the scanner is processed by the controller. It cuts the production stoppages and reduces second quality fabric. It distinguishes between the needle faults and holes more precisely than the human eye and saves a lot of time and money.
“High standards are followed in the manufacturing processes to impart a longer life to our products. We also guarantee the spare parts’ availability for 10 years. This makes the buyers to use our products for a long time,” says Stefan Maier, Area Sales Manager, Memminger.
Apart from scanner, the company offers a range of feeders and it includes MPF P & MPF L-Positive Feeder, MSF 2 & SFE-Storage Feeder, EFS 800 & EFS 900-Electronic Yarn Feeder and MJS 2-Striper Feeder. “Our feeders increase the productivity by 20 to 25 per cent as compared to other normal feeders,” says Maier.
“All the authorized dealers in the country are well experienced to explain the products to the customers and if needed they get trained from Germany based technicians,” concludes Maier.