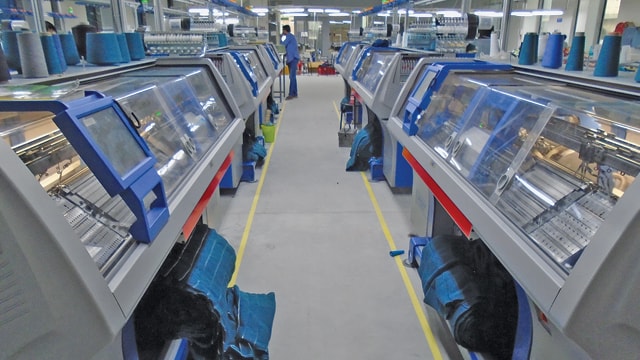
In apparel manufacturing industry, there are two kinds of business. One is commodity business which includes standard products catering to masses where volumes are high, the product is standardized with sharper prices and challenges. The other one is the niche business having captivating product designs coupled with value additions in the garments. Niche normally has lesser quantities with more variants and great margins; yet it is not something garment manufacturers are putting their hands in. But this scenario is completely different and evolving for the Greater Noida-based garment manufacturing start-up KatBro Corporation. “We had already decided to go for the fine gauges as these are difficult to handle but, frankly speaking, no one in India is even thinking about it,” claims Chandra Bhan.
Riding on the crest of confidence was never easier for KatBro as there has already been an existence of big names in the market having long-held supremacy in niche manufacturing. But the think tank of the company, Chandra Bhan grabbed the potential sector in knitting, i.e. flat knitting, towards which very few manufacturers in India are dedicated. “All the exporters are active either in course gauges or in circular knitwear. Flat knitting, that too in fine gauges, is not yet developed in India because of its complicated handling. Otherwise it is not something that is known to me only,” comments Chandra Bhan.
With a thought of doing something India is not known for in knit products manufacturing, Chandra Bhan Kataria, Owner, KatBro Corporation visited ITMA’15 in Milan just to have a pulse of the global market. The offerings in the trade show were irresistible for the KatBro team and they decided to venture into knitwear manufacturing business which led to the origin of KatBro Corporation. “I always wanted to make an IT-enabled garment manufacturing unit with niche concept and, proudly speaking, I have started it,” shares Chandra Bhan.
Aiming to transform the conventional idea of knitwear as a winter product, KatBro is focusing on ‘Summer Knitwear’ products and has automatized each and every manufacturing process inside the factory. A dedicated SDS Apex 3D design studio by Shima Seiki for design development helps the company in designing new styles in comparatively much lesser time.
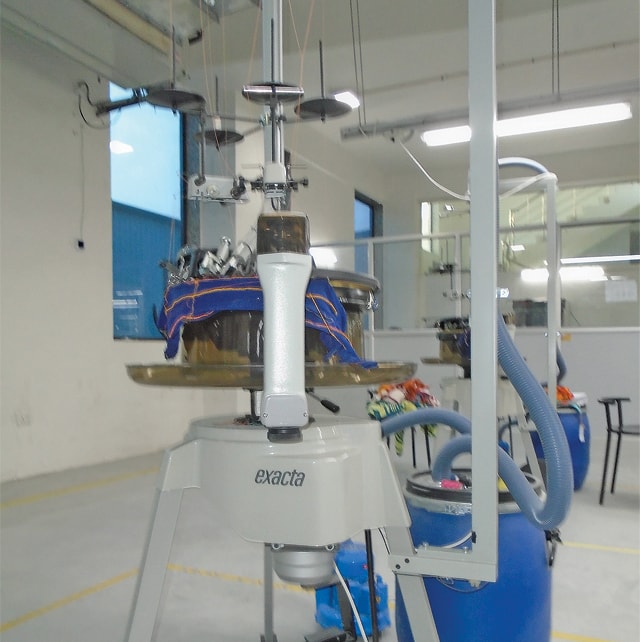
Revolving around the tagline ‘We Craft Luxury Fashion’, KatBro uses supima yarns, micro modal, linen, cashmere, merino, coolmax, thermolite, miyabi and various blends which are pretty uncommon to find in the Indian market. For the best of the quality in its products, KatBro uses Huntsman dyes.
Once the designs are developed, the company approaches the next level to knitting by installing 12 advanced Stoll CMS 530 HP flat knitting machines having 18 gauges linked with programming and networking. With a working width of 127 cm and three systems, the CMS 530 HP enables KatBro to knit complex patterns quickly and productively. “Its optimal combination of ‘knit/transfer/knit’ with structured distribution and racking patterns boost production effectively reducing complexities of the knitting process,” shares Chandra Bhan.
Furthermore, the production floor of KatBro is equipped with the state-of-the-art Juki Sewing machines. In addition, these machines have digital feed system which eases operator’s strenuous efforts in achieving accuracy at the optimum level.
Appreciating the technology and realizing the importance of cleanliness, every Juki sewing machine has an attached piping system at the end of the overlock machines, where the trimmed fabric directly goes into the in-built vacuum system that not only eliminates the use of mask for the operators but also maintains cleanliness.
Apart from the sewing operation, linking operation is also considered as a crucial one for knit products. Therefore, KatBro joined hands with the Italian linking machine manufacturing giant Exacta to install ULTRAVISION and QUASAR models. With eye needle inside the point dial and traditional looper, the knitwork is linked from the reverse side in the ULTRAVISION machines. The machine also permits to obtain a very elastic chainstitch whereas, QUASAR model enables the manufacturer for the quick imitation of linking of round or V-neck knit products with automatic feeding unit of the trim.
“These machines are not something as even big exporters are installing, but we know the required quality level of products for niche manufacturing…, These are a must for us, and thus, we did not hesitate even once to invest in these machines,” says Chandra Bhan.
The journey has been incredible so far…
Working for big names in apparel industry such as Ed Hardy; Benetton; Nautica and Arrow of Arvind brands; Louis Phillipe; Van Heusen and Allen Solly of Madura; Biba and ITC Wills within just three months of its inception, KatBro is highly motivated in its growth path.
But getting orders from these brands in such a less time was a major challenge for the company. “During discussion with ITC Wills, they told me that they have dropped one article as its manufacturing is not possible in India. I asked them if garment has already been manufactured, it means that somebody has done it and if somebody has done it, why can’t we…,” underlines Chandra Bhan, adding, “We then got the sampling order for that design and manufactured it in three days and asked them to differentiate which was theirs and which was ours.”
Young forces adding vibrancy and bringing enthusiasm…
The GenNext at KatBro has not replaced the older generation at KatBro, but is working along with Chandra Bhan supporting him with their new and innovative ideas and out-of-the-box thinking. Ready to take on the challenges, Shubham Kataria, COO and Kunal Kataria, CEO, of the company are passionate brothers who aim to take the organization to a whole new level in the coming years.
Manufacturers adopt technology for ease in production and to reduce labour cost but, besides adopting automation for production, KatBro took to technological measures to keep its attrition rate at zero per cent till date.
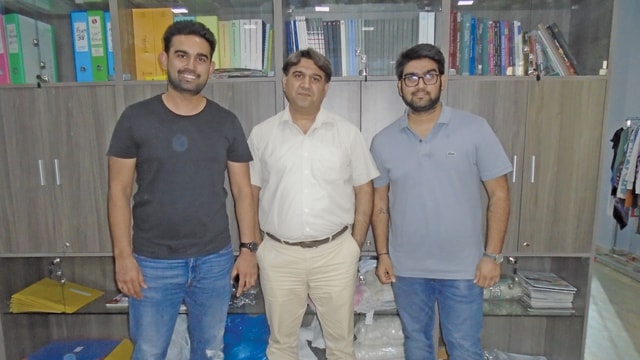
Corresponding technology with sustainability, Shubham explains, “We built our factory with no pillars inside providing a 360-degree view throughout. The design itself is special as there are no pillars and heavy beams within the 60 feet area of the unit, rather it’s made with ‘post-tension beam technology’. In addition, the entire floor is constructed with aerated bricks which act as heat insulators. The production floor is also equipped with an air conditioner… If our people work in such an environment, then there is no point of losing our operators.”
As of now, the running factory with 45 highly-skilled workers and the entire workforce have got training in-house only on how to operate such advanced machines. “Since the Indian market is more familiar with 12 and 14 gauge knitting machines, there was a need to train operators as per our machines, thus we put them under on-job training of 16 and 18 gauges in our own unit,” shares Kunal.
A long way to go…
This high-tech company still believes that there is way more to do in knitwear and technology. The company has already invested in ‘Garment Knit Software’ (GKS) to simplify and improve the grading process. Once installed, KatBro will replace manual grading method.